Pneumatic Components in Industrial Automation
Pneumatic components are essential elements in industrial automation systems, leveraging compressed air or gas to transmit and control power. These components enable the operation of a wide range of industrial machines and equipment, ensuring efficient, reliable, and precise mechanical actions.
Main types of pneumatic components
Pneumatic systems are composed of several fundamental components that work together to manage airflow, provide power transmission, and ensure system reliability.
Pneumatic Cylinders: These devices convert the energy from compressed air into mechanical motion, typically linear or reciprocating movements. Cylinders are widely used for applications requiring precise and repetitive motion, such as material handling and robotic arms.
Pneumatic Valves: Valves regulate the direction, pressure, and flow of compressed air within the system. They are crucial for controlling the movement of actuators and other mechanical devices.
- Directional Valves: Control the direction of airflow, often allowing for multi-directional control of actuators.
- Logic Valves: Make decisions based on pneumatic signals, facilitating more complex control schemes.
- Quick Exhaust Valves: Enable rapid venting of compressed air, increasing the speed and efficiency of pneumatic actuators.
Solenoid Valves: Solenoid valves are electromagnetic valves that control the flow of compressed air. They are among the most critical components in pneumatic systems, enabling precise and automated control over airflow and pressure. These valves are used in conjunction with electrical controls to regulate the operation of actuators.
Air Preparation Units: These components ensure that the air supplied to the pneumatic system is clean, dry, and properly regulated. They include filters, regulators, and lubricators, collectively known as FRL units (Filter, Regulator, Lubricator). Proper air preparation enhances the performance and longevity of pneumatic systems by removing contaminants such as moisture, oil, and particulates.
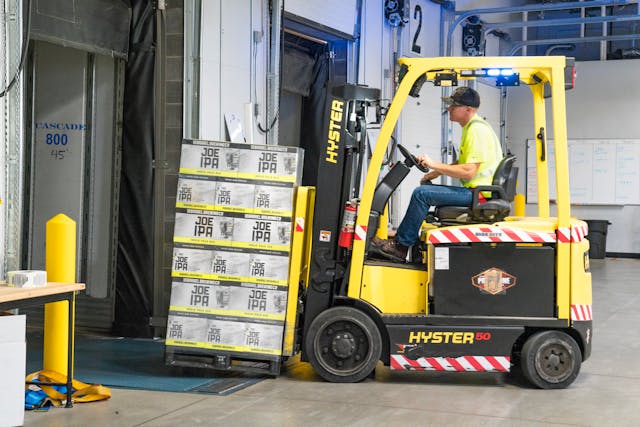
Photo by ELEVATE on Pexels
Vacuum Ejectors: Vacuum ejectors are specialized pneumatic components used to generate vacuum pressure by utilizing compressed air. This component creates suction by expelling air at high speeds through a venturi nozzle, making it crucial for applications such as material handling, pick-and-place systems, and packaging automation.
Pneumatic Tubing and Fittings: Tubing and fittings connect different components within a pneumatic system, ensuring a leak-proof transfer of compressed air. Common types of fittings include connectors, couplings, adapters, and quick-release fittings, which ensure secure connections and easy maintenance.
Applications of Pneumatic Components in Industrial Automation
Pneumatic systems are employed across a wide array of industries due to their reliability, cost-effectiveness, and simplicity. Key industries include:
Food Processing: Pneumatic components are used in tasks such as filling, capping, and packaging, where sanitary conditions and precise control are essential.
Packaging: Automation in the packaging industry heavily relies on pneumatic systems for sorting, sealing, and assembling products at high speeds.
Textile Industry: Pneumatic systems are involved in tasks like weaving, spinning, and dyeing, offering precision and durability in demanding environments.
Pharmaceutical Industry: Pneumatic systems ensure precise control in delicate processes like filling vials, capsule manufacturing, and packaging.
Lithium Battery Manufacturing: In advanced manufacturing environments, pneumatic systems assist in precise and synchronized tasks that require consistent quality control.
For example, in automatic liquid filling equipment, a common failure point can be the solenoid valve coil. A malfunction in this component can lead to operational breakdowns, necessitating timely replacement to restore functionality.
Functions and Capabilities of Pneumatic Systems
Pneumatic components enable a wide range of functions essential for industrial automation. These include:
Switching Pneumatic Signals: Managing signal flows to control machine actions.
Pressure Regulation: Ensuring consistent system pressure, essential for safe and reliable operation.
Overload Protection: Preventing system damage by protecting equipment from excessive pressure or mechanical stress.
Air Filtration: Removing moisture, oil, and solid particles from compressed air to maintain system cleanliness.
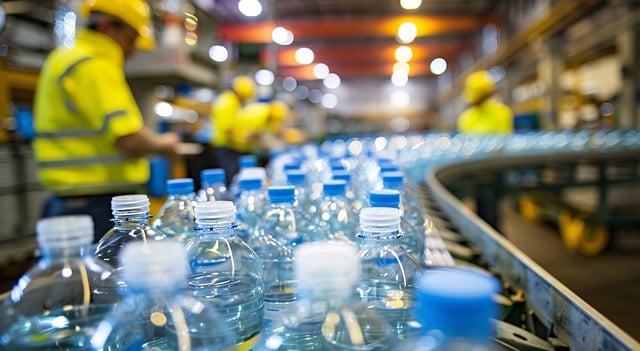
Image by GrumpyBeere from Pixabay
Flow Direction Control: Ensuring precise direction and control of airflow for efficient system operation.
Vacuum Creation: Vacuum ejectors provide a highly efficient way to generate suction for handling delicate or lightweight materials in pick-and-place applications.
In specific applications like blow molding machines, pneumatic components assist in multiple steps, including feeding, locking, stretching, high-pressure blowing, deflation, and the removal of finished products, such as plastic bottles.
Advantages of Pneumatic Components
The advantages of pneumatic components in industrial automation are numerous, making them a popular choice for a variety of applications:
Simplified Design: Pneumatic systems are mechanically simple, with fewer moving parts compared to hydraulic or electrical systems.
Durability and Long Service Life: Pneumatic components are designed to operate in harsh environments, offering long-lasting performance with minimal maintenance.
Reliable Overload Protection: Pneumatic systems provide inherent protection from overloads, ensuring safe and continuous operation.
Environmental Cleanliness: The use of compressed air ensures no environmental contamination, making pneumatic systems ideal for sensitive industries like food processing and pharmaceuticals.
Fire and Explosion Safety: Pneumatic components operate safely in flammable or hazardous environments since they do not rely on electrical currents or combustible fluids.
Synchronized Energy Supply: Pneumatic systems can efficiently supply multiple points of use simultaneously, facilitating complex automation processes.
Vacuum Efficiency: Vacuum ejectors offer an efficient, low-maintenance solution for generating suction without the need for bulky or expensive vacuum pumps.
Choosing High-Quality Pneumatic Components
When selecting pneumatic components, the specific requirements of the automation system should be considered. Such as rated pressure, flow rate and application environment. In addition, the performance and reliability of a pneumatic system depends greatly on the quality of the components. Manufacturers need to continuously optimize pneumatic components to improve durability and reliability and upgrade product features. It is crucial to choose a manufacturer that specializes in pneumatic components and offers comprehensive warranty and after-sales support.
To learn more, we recommend contacting Ningbo VPC Pneumatic Co., Ltd. Their technical experts will answer your questions and provide the best solutions.